Never giving up was the most valuable lesson three friends learned from a recent vehicle building project.
Hauraki Plains College students and brothers Billy Grimmer, 16, Daniel Grimmer, 14, and their friend Josh Hansen, 14, told The Profile they spent months and months working on their project, which “paid off” in the end.
The young minds put their heads together to do something they’d never done before: build a kart powered by an electric motor.
But it didn’t stop there.
The trio, known as the Battery Burners, raced their electric kart in the Waikato/ Bay Of Plenty Regional Final for the EVolocity Challenge in Rotorua on October 22, and snapped up third place in the competition, third place for the engineering design award, and third overall for vehicle performance, as well as a certificate of achievement.
EVolocity is an organisation which seeks to break down barriers and inspire rangatahi or young people into sustainable engineering through mentorship and being part of their EV programme.
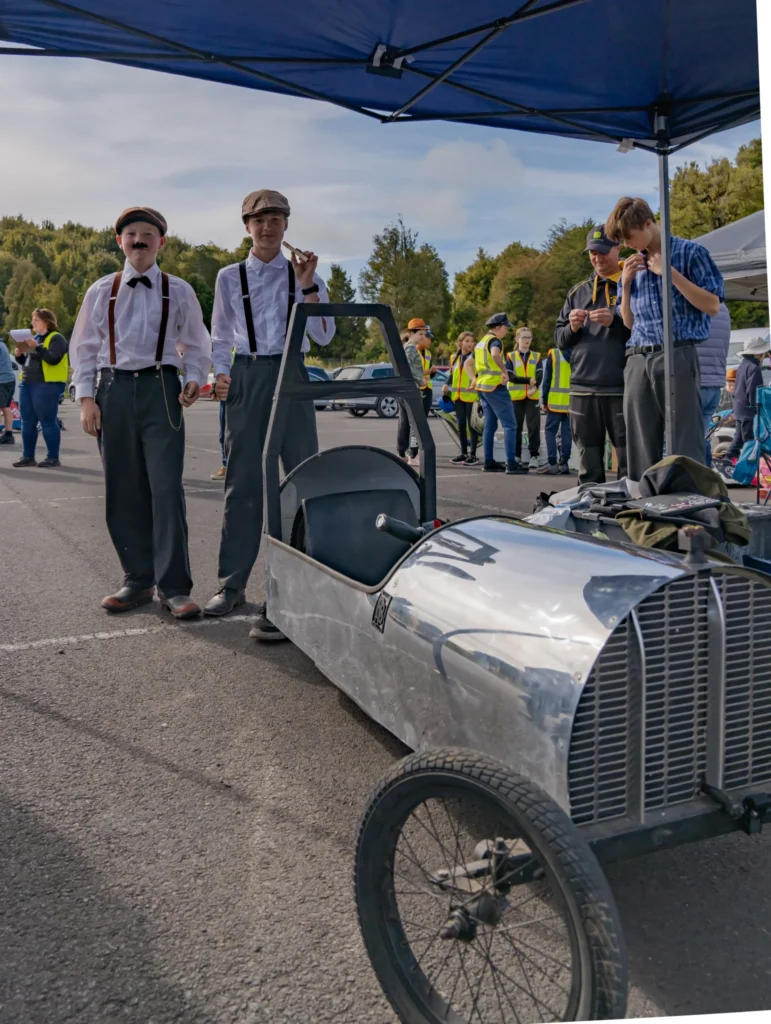
The young engineers heard about another school taking part in the EVolocity Challenge, so decided to get involved, they said.
Racer Daniel said he and Josh took turns driving the kart in the slalom, drag and endurance races.
Their high ranking and recognition meant a lot to them.
“We thought it was amazing because we’ve never done it before,” they said.
But putting the kart together took a lot of teamwork and trialing to get things right.
Daniel said they planned out a 3D model using a computer-aided design (CAD) software system called Onshape, and built from that as their draft.
The materials they used to build the kart were: 3D printed plastics, recycled aluminium sheets, recycled plywood, grill, handlebars, wheels, gears, some of the frame, seat, and the new motor, which was sent by EVolocity, they said.
“[The] brake cable was new and our only expense.”
After its initial testing, the most significant adjustment the group made to the kart was to the steering wheel and brakes, they said.
“Our welding was not the best as the steel was so thin, which made it really hard. So we put a bigger weld on.”
Moulding the sheet around the back of the car and measuring the angles was the biggest challenge, Daniel said.
But the most exciting part of the process was once it was all together and they could drive it, Billy said.
Their advice for other students, who are thinking about starting a similar project was simple: “measure twice and cut once”.